Surface Treatment Service
Anodizing Service
Anodic oxidation as a new anodic oxidation technology, magnetic powder such as Fe3O4, CrO2, TiO2, superhard powder such as Al2O3, SiC, SiN, and conductive powder such as graphite (micron level) are added to sulfuric acid, oxalic acid, and trisodium phosphate electrolyte respectively to suspend them in the electrolyte for anodic oxidation. This process has the advantages of easy operation, simple equipment, and low cost. Compared with conventional anodic oxidation, its oxidation speed, upper operating temperature, and film performance are significantly improved.
Advantage
1. Anti-corrosion. The stroke of the oxide film can cut off the contact between air and aluminum profiles, so as to prevent corrosion.
2. Prevent STATIC electricity. In addition to corrosion resistance, the oxide film can also prevent static electricity. So a lot of anti-static workbench, clean shed like to use communication aluminum to make, can reduce the adhesion of dust, easy to clean. Industrial aluminium section
3. Beautiful and generous. After anodized industrial aluminum profiles, the surface is bright as new and the service time is long. Used to make equipment cover, protective fence and so on, beautiful and generous. And oxidation can have a lot of colors to choose from, such as champagne, steel and so on, reflecting the decorative role of aluminum profiles.
4. Health and safety. Profile after surface treatment, the late will not paint, will not produce formaldehyde and other gases, health and safety, low maintenance cost.
Sandblasting Service
Shot blasting cleaning is a kind of non-contact cleaning using high-speed projectile from a long distance. The process is not limited by the size, shape, and weight of the workpiece to be cleaned. Small to screws, nuts, large to train carriages, ten thousand tons of ship shell, Simple to a flat plate, complex to the engine cylinder cooling water jacket, From a few grams to a million tons, shot blasting can be used for cleaning.
Shot blasting cleaning is to use the centrifugal force of the impeller on the head of the shot blasting machine at high speed to shoot the abrasive at a high linear speed to the surface of the steel to be treated, to strike and grind, to remove the oxide skin and rust on the surface of the steel, and to produce a certain roughness.

Request a Quote
"*" indicates required fields
Advantage
1. Cleaning strength – the so-called shot blasting cleaning machine is to use mechanical equipment to our steel sand or steel shot for high-speed projection, high-speed drop strength can clean the surface of the workpiece. In order to be able to more effective and meticulous cleaning each part of the workpiece, a shot blasting cleaning machine is used by centrifugal operation, to ensure that each part.
2. Long service life – we also mentioned above the working principle of the shot blasting cleaning machine, the use of high-speed steel shot to use the speed of decline to the workpiece pile foundation and achieve the effect of cleaning. In order to meet the work needs of the shot blasting machine, a protective plate will be added to the heat insulation area of the cleaning room to protect the memory of the shot blasting machine.
3. low cost – due to the needs of its work, the shot blasting machine is installed with several different supporting equipment, so as to ensure that there will be no errors in the operation process.
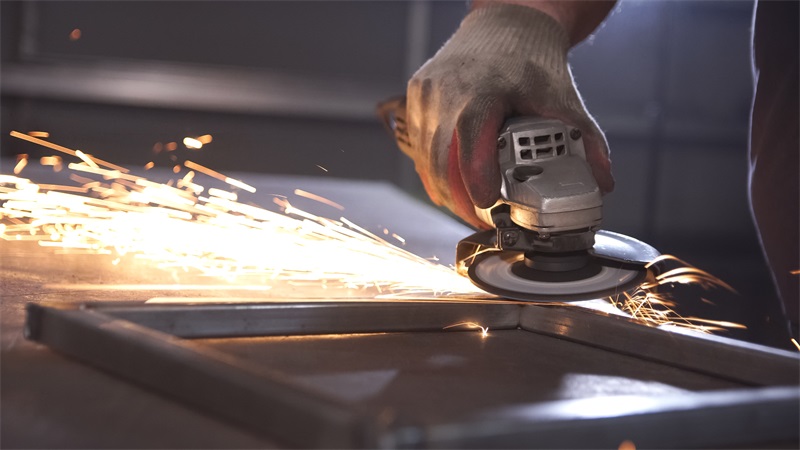
Polishing Service
Polishing is a polishing method to remove the smooth surface of the convex part by polishing after the plastic deformation of the material surface is removed. Commonly used items include oilstone, rough wheel, sandpaper, etc., which are mainly operated manually. For the rotation of special parts such as solid surfaces, tools such as a rotary table can be used, and the super grinding method can be used for those with high surface quality.
Advantage
1. Environmental protection, nano polishing liquid is very environmental protection, the waste liquid can be directly discharged without causing pollution, and can also be slightly treated and recycled. And no pollution to the processing environment, adapt to the development direction of green manufacturing.
2. Simple operation, plasma nano polishing adopts special automatic control equipment, simple operation, convenient maintenance.
3. Low cost, low processing costs, is conducive to the promotion, and can reduce the number of workers, and reduce labor costs. At the same time, it can also save many material consumptions caused by artificial mechanical polishing, electrolytic polishing, chemical polishing and other traditional polishing methods for customers.
4. High efficiency, automatic control equipment through special agents can achieve mirror electroplating effect in ten seconds to two minutes, greatly improve the production efficiency.
Electroplating Service
The process of attaching a metal film to the surface of a metal or other material by means of electrolysis. It can prevent corrosion, improve wear resistance, electrical conductivity, reflectance, and enhance aesthetics.
The purpose of electroplating metal coating is to electroplate the substrate. Changing the surface properties or dimensions of the substrate can enhance the corrosion resistance of the metal coating (coating the metal coating with corrosion-resistant metal), increase the hardness, prevent wear, improve the conductivity, lubricity, and heat resistance, and make the surface beautiful.
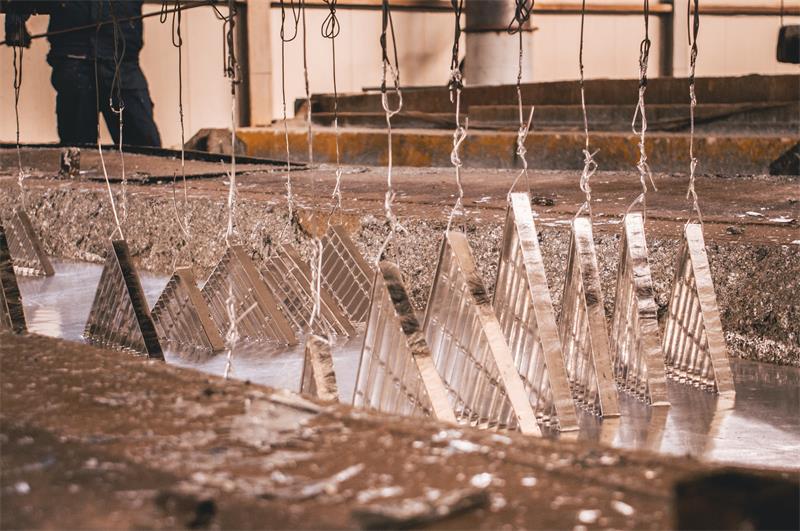
Advantage
1. Improve the corrosion resistance of metal products or parts. Such as steel products or parts surface galvanized.
2. Improve the protective – decorative performance of metal products. For examples, copper plating, nickel plating, and chromium plating on the surface of iron and steel products.
3. Repair the size of metal parts. Such as shaft, gear and other important mechanical parts wear after use, can use iron plating, chromium plating, and other dimensions.
4. Electroplating can also give products different functions. Chrome plating, such as improves the wear resistance of the product itself.
Powder Coating Service
Spray is the powder coating installed in the container through compressed air to the nozzle, in the nozzle front will generate high voltage static electricity and the formation of an electrostatic field. When the coating powder passes through the electrostatic field, it will discharge to them, and each powder will become charged coating ions. Under the action of electrostatic force, after being ejected, it will be attracted by the opposite polarity of the product, so as to adsorb on the product surface.
Advantage
1. Spraying process without diluent and construction of no pollution to the environment.
2. Coating appearance can meet a variety of different requirements of customers, mainly matte, high gloss, flash gold, crack, orange grain, frosted, etc,.
3. electrostatic spraying without primer, greatly improve the processing efficiency.
4. The cost is lower than the spray paint processed into the same effect, and it is more resistant to corrosion, aging and high adhesion.
Request a Quote
"*" indicates required fields