Aluminum Die Casting Service
What is Aluminum Die Casting?
Aluminum die casting is a kind of pressure casting part.
It uses a pressure casting machine equipped with a casting mold to pour the aluminum or aluminum alloy heated to liquid into the feed inlet of the die casting machine.
After die casting by the die casting machine, aluminum parts or aluminum alloy parts with limited shape and size of the mold are cast.
Such parts are usually called aluminum die casting.
Benefits of aluminum die casting services
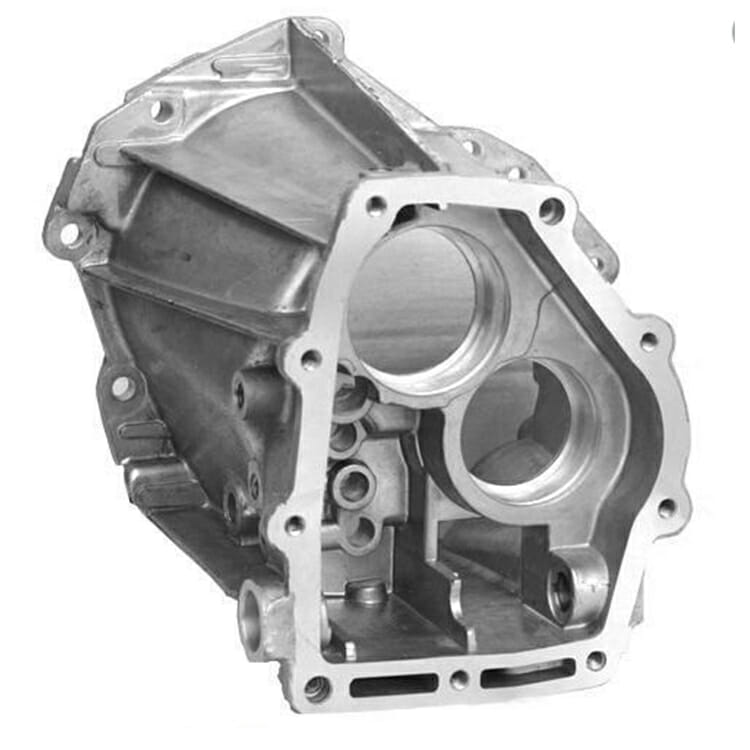
Request a Quote
"*" indicates required fields
Heat treatment for aluminum die casting services
The heat treatment of aluminum castings is usually divided into three steps:
1. Solution treatment of aluminum die castings:
The aluminum casting is heated to the eutectic melting point, held at this temperature for a corresponding time, and then rapidly cooled. The goal is to make the fortifying ingredients dissolve well.
Solution treatment can improve the strength and plasticity of aluminum castings and improve the corrosion resistance of aluminum alloys.
The effect of solution treatment of aluminum castings is usually related to temperature, holding time and cooling rate.
2. Aging treatment of aluminum die castings:
The aging treatment of aluminum castings can be divided into artificial aging and natural aging.
Artificial aging of aluminum castings: The aluminum castings after solution treatment should be heated to the set temperature, discharged after a period of time, and slowly cooled in the air, which is called T6.
Natural Aging of Aluminum Castings: Aging (T5) is done at room temperature. Natural aging time is long, generally not selected.
Aging treatment is a spontaneous decomposition process of supersaturated solid solution of aluminum castings, which can restore the lattice of the alloy matrix to a relatively stable state.
3. Annealing:
The process of heating the aluminum die-casting to 300°C and cooling it to room temperature in a furnace after holding for a period of time is called annealing.
During the annealing process, the solid solution of the aluminum casting is decomposed and the phase particles are aggregated, which can effectively eliminate internal stress, maintain dimensional stability, prevent deformation and enhance plasticity.
Benefits of heat treatment of aluminum die castings parts:
1. Homogenization of alloying elements – this is an element uniformly distributed throughout the matrix, so the performance of the casting will be uniform.
2. Stress relief – the generation of residual stresses during high-temperature casting and cooling at solution temperature. These residual stresses can be reduced by heating the casting to the intermediate temperature.
3. Improved dimensional stability and machinability – changes in microstructure may cause castings to grow over time. Maintain tight dimensional tolerances during and after machining, and the castings shall be heat treated to form a stable precipitate phase.
4. Mechanical property improvement – the greatest use of heat treatment is to enhance mechanical and corrosion properties by spheroidizing constituent phase particles and precipitation hardening.
Very few of the required properties are optimized in a single die casting parts. More often, heat treatment is a compromise that maximizes the use of other properties. For example, tensile strength and yield strength can be increased, but this results in lower elongation. Conversely, higher elongation results in lower tensile and yield strengths.
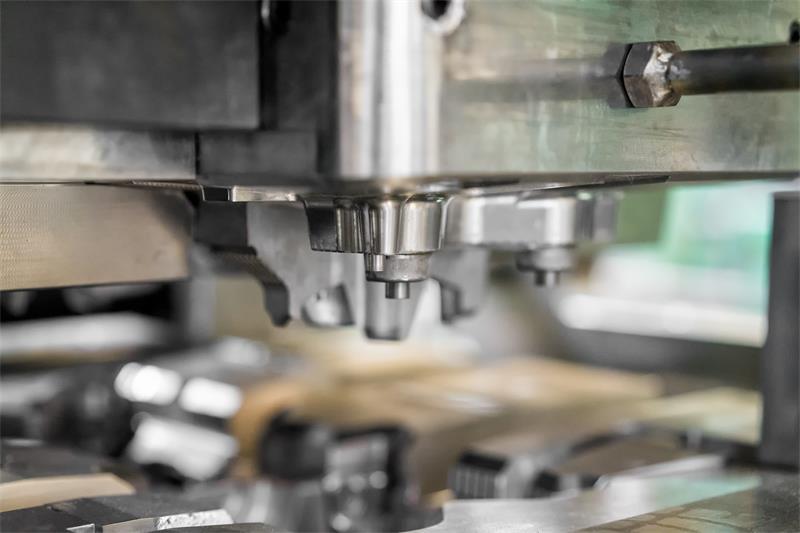
Aluminum zinc die casting capabilities
Aluminum die casting is cold chamber die casting, and zinc die casting is hot chamber die casting, both of which belong to precision die casting. The process flow and principle are very similar. Our factory has 4 cold chamber die casting machines, 3 hot chamber die casting machines and more than 20 CNC machining centers. We provide one-stop services from mold making, proofing, production, packaging and transportation to ensure the smooth progress of customers’ projects in professional guidance and cooperation.
Why Choose AIKEHAN Aluminum Die Casting Services
1.Professional manufacturer
Aluminum die casting process is to pour the molten liquid of aluminum alloy into the mold and solidify into castings under pressure.
We have great equipments and a manufacturing team composed of experienced workers, who ensure the quality of products.
Factory with 180-1260 tons of cold die casting machine, using high pressure casting. Our products not only have high surface tolerance grade, good roughness and high strength, but also have high production efficiency, at least 50000 pieces per month.
Factory equipment:
Die-casting machine with 180 tons to 1260 tons of robots, 12 CNC machining centers, 20 CNC lathes, automatic drilling and tapping machine, vibration grinding machine, shot blasting machine, laser typewriter, CNC turning, electric pulse, wire cutting, milling, grinding, CMMCompetitive price and Free samples
2.OEM/ODM service
3.Certificates
We have ISO,TUV and IATF16949 certificates.
4.QC and after-sales service
Our product scrap rate is controlled within 2%. At the same time, we are also equipped with a CMM to detect and control the product tolerance and size within the range of customer requirements,and it’s toelrance is 0.0005.We will inspection 100% before shipping.We also provide assembly service if customers requires.
We will ship free samples to our customers to confirm before batch production,In case of product quality problems, we will bear the corresponding losses after inspection and confirmation that it is a problem in our production process.
The differences between aluminum gravity die casting and aluminum pressure die casting
Aluminum alloy die castings characteristics:
1. Good surface, generally reaching ra6.3 or even Ra1.6.
2. The product has high air tightness, high casting strength, and surface hardness, but low elongation.
3. The mold has high cost and short service life.
4. High productivity.
5. It can produce thin-walled parts with small machining allowance.
Aluminum alloy gravity castings characteristics:
1. The product surface is not smooth, and it is easy to produce pits after shot blasting.
2. The castings aluminum parts have few air holes and can be heat treated.
3. The product has low density, and slightly poor strength, but high elongation.
4. The mould has low cost and long service life.
5. Low production efficiency increases production costs.
6. The process is relatively simple, which is not suitable for the production of thin-walled parts.
Gravity casting of aluminum alloy refers to the process of injecting molten aluminum into the mold under the action of the earth’s gravity. Gravity casting is divided into sand mold casting, metal mold (steel mold) casting, lost foam casting, etc.
The most widely used mold is steel mold, castings are made of heat-resistant alloy steel. The strength, size, and appearance of cast aluminum castings are higher than those of other casting processes.
The aluminum melt of gravity casting is usually poured manually. It relies on the self-weight of molten metal to fill the cavity, exhaust, cool, and open the mold to obtain samples. The process flow generally includes molten aluminum smelting, casting filling, exhaust, cooling, mold opening, production cleaning, heat treatment, and processing.
Request a Quote
"*" indicates required fields